Exploring the P and Q System of Inventory Management
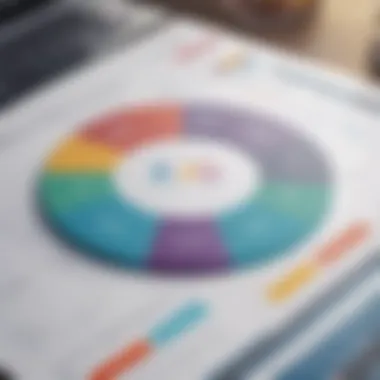
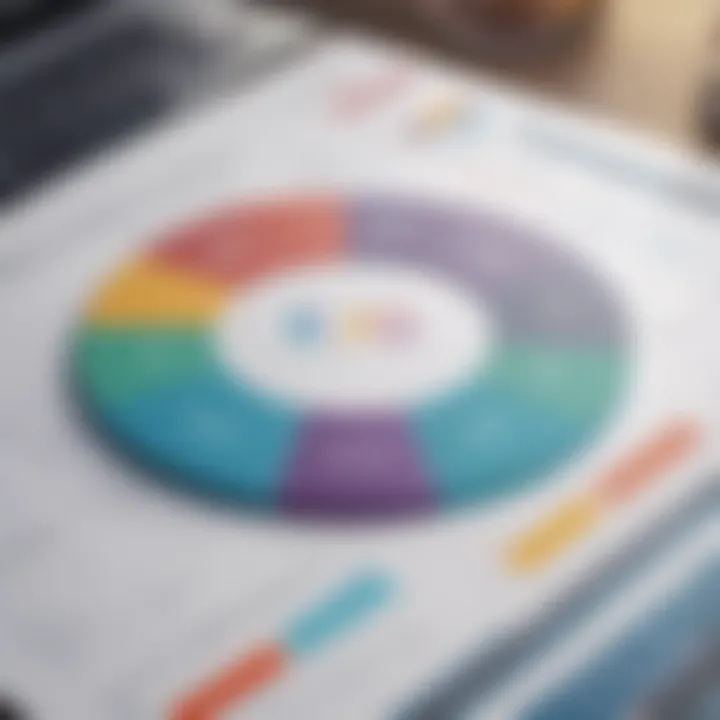
Intro
In today’s fast-paced market, managing inventory effectively is more than a back-office task; it’s a strategic advantage. The P and Q system, commonly used in inventory management, presents an analytical approach that many organizations find beneficial for maintaining optimal stock levels while keeping costs in check. Understanding this system can significantly enhance operational effectiveness and financial health.
The P and Q framework provides a way of balancing the need for products to meet customer demand with the costs associated with holding stock. It encourages businesses to refine their inventory strategies deeply. By examining key principles and practical implementations, organizations can see significant improvements. This article lays out the fundamentals of the P and Q system, discussing its mechanics, advantages, and potential downsides.
We'll also explore how to effectively integrate this system into current inventory strategies and how economic conditions and technological advancements shape these processes. As we navigate through this in-depth discussion, readers will gain insights that can lead to practical applications in their businesses, driving not just efficiency but also profitability.
Investment Dictionaries
Understanding Key Terms
In the context of the P and Q inventory system, it's vital to familiarize ourselves with some foundational terminology:
- P System: This refers to a continuous review strategy where inventory levels are constantly monitored. A new order is placed when stock reaches a set reorder point.
- Q System: This is a periodic review system where inventory is checked at set intervals, and stock is replenished to a predetermined level.
- Safety Stock: An additional quantity of inventory kept to mitigate the risk of stockouts caused by uncertainties in supply and demand.
- Lead Time: The period between placing an order and receiving the goods.
- Economic Order Quantity (EOQ): This is the ideal order quantity a company should purchase to minimize inventory costs, considering factors like demand rate and ordering costs.
Common Inventory Management Strategies
To successfully implement the P and Q system, one must be aware of common strategies utilized in conjunction with it:
- Just-In-Time (JIT): This strategy aims to minimize inventory levels and increase efficiency by receiving goods only as they are needed.
- ABC Analysis: This method categorizes inventory into three groups, A, B, and C, based on their importance and value to the business.
- Vendor Managed Inventory (VMI): Here, the supplier assumes responsibility for managing the inventory levels of their products at the customer's location.
Effective inventory management blends strategy with execution, ensuring that businesses can respond swiftly to changing market conditions.
Staying informed about these terms and strategies can empower organizations to implement the P and Q system efficiently. The benefits of such a strategic approach can set a company apart in a crowded marketplace, paving the way for greater profitability and customer satisfaction.
As we delve deeper into the operational mechanics and benefits of the P and Q system in the following sections, keep in mind these foundational elements. They will help frame our analysis and guide practical application.
Foreword to P and Q System
The P and Q system stands out as a meticulous method for managing inventory, particularly for organizations that strive for efficiency and cost-effectiveness. In the world of business, maintaining the right balance of stock can spell the difference between profitability and financial losses. Companies face the continuous challenge of minimizing costs while ensuring that products are readily available for customers. This is where the P and Q system comes into play, providing a structured approach that aligns inventory management with broader business objectives.
Definition and Overview
The P and Q system of inventory management essentially revolves around two vital components: periodic review and continuous review. In simpler terms, 'P' refers to the moment a company assesses its inventory at specific intervals, while 'Q' denotes the ongoing scrutiny of stock levels. This dual strategy offers businesses a robust framework to gauge their inventory status, thus facilitating timely decision-making.
An understanding of the P and Q system is crucial for various stakeholders, from supply chain managers to financial advisors, as it has the potential to optimize stock levels and improve bottom-line results. Not just businesses, even startups can derive significant advantages from employing this model—removing the uncertainty surrounding inventory management. It’s about having the right product, in the right quantity, and at the right time, which, let’s face it, is the holy grail of inventory control.
Historical Context
To appreciate the P and Q system, it's essential to grasp its origins and evolution over time. The concepts behind this system emerged amidst the need for better stock management techniques as businesses began to scale their operations. Historically, inventory management was haphazard, often leading to excesses or shortages that could thwart operational efficiency.
In the early 20th century, manufacturers faced enormous challenges related to stockouts and wasted resources, leading to the birth of various inventory control methods. The Economic Order Quantity (EOQ) model emerged as a significant player in this arena, emphasizing the importance of optimal ordering to reduce costs. However, as markets became more dynamic, the limitations of EOQ became clearer, particularly in its inability to adapt to changing demand patterns.
Thus, the P and Q system evolved as a hybrid approach, offering flexibility with periodic checks (the P approach) and the constant evaluation characteristic of the Q method. This innovative blend allowed businesses to respond rapidly to market fluctuations while also keeping an eye on cost-efficiencies.
The adaptability of the P and Q system has created a ripple effect across industries. Organizations experienced improved stock management, leading to greater customer satisfaction and streamlined supply chains, illustrating its relevance even in today’s fast-paced economy. As technologies continue to advance, knowledge of the P and Q system will prove increasingly valuable, making it essential for professionals in the financial sector and beyond to grasp its fundamental principles as they navigate modern inventory challenges.
Core Concepts of the P and Q System
The core concepts of the P and Q system serve as the bedrock for effective inventory management. Understanding these foundational elements is crucial for businesses aiming to optimize stock levels while controlling costs. The P and Q framework addresses two distinct approaches: periodic review and continuous review. By grasping these concepts, companies can tailor their inventory strategies to meet specific operational needs and market demands.
Understanding 'P' – Periodic Review
The periodic review aspect, denoted as 'P,' revolves around assessing inventory at fixed intervals. Think of it like setting a calendar reminder to check your pantry every two weeks. This systematic evaluation allows businesses to take stock, literally, of their inventory and make decisions based on current conditions.
When employing a periodic review, the following points are often considered:
- Fixed Review Cycle: The business determines how often reviews will occur, which can range from weekly to monthly. This consistency establishes a rhythm for inventory checks.
- Optimal Order Quantity: After evaluating current stock levels and projected needs, firms decide how much to order. The goal is to maintain enough product to meet demand without overstocking.
- Lead Times: Understanding the time it takes for products to arrive once ordered is essential. If a supplier typically takes a week, it's important to account for that duration when determining how much to stock.
One notable advantage of this system is its straightforward nature. Businesses can strategically plan inventory replenishments, preventing stockouts or excess inventory. However, organizations must be cautious, as insufficient data or sporadic assessments can cloud judgment about actual needs.
Understanding 'Q' – Continuous Review
On the flip side, 'Q' represents continuous review, which takes a more agile approach to inventory management. It resembles having a constant eye on shop shelves, ensuring that products are replenished as they are sold. This method allows businesses to respond swiftly to fluctuations in demand, making it particularly valuable in today’s fast-paced market.
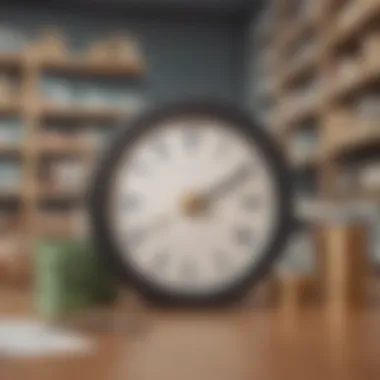
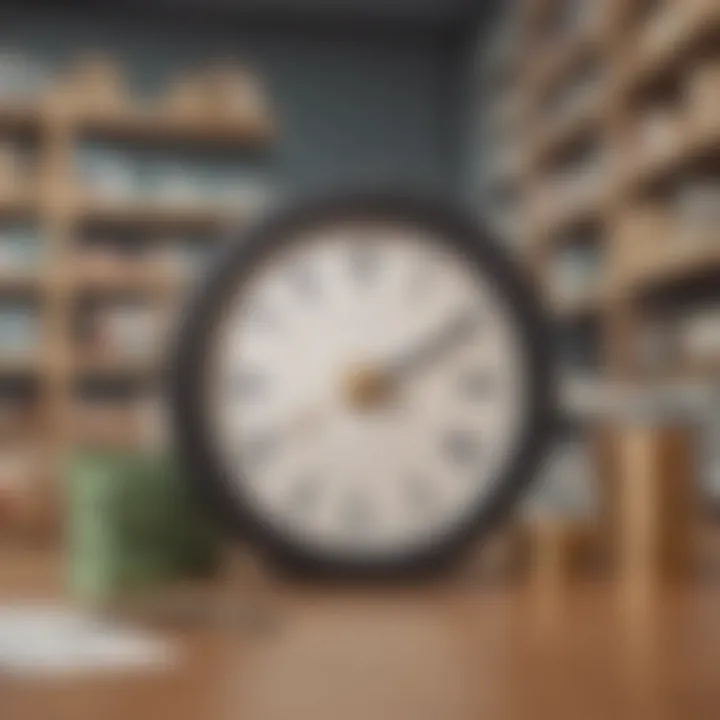
Key elements of continuous review include:
- Real-Time Monitoring: Businesses track inventory levels continuously. When a preset reorder point is reached, orders can be placed immediately.
- Dynamic Order Quantities: The amount ordered can vary depending on current stock levels, lead times, and projected sales. This flexibility helps maintain a lean inventory.
- Management of Stockouts: By constantly assessing inventory, firms mitigate the risk of stockouts, ensuring customer demand is consistently met.
Both periodic and continuous reviews have their merits, and understanding these concepts allows organizations to choose the method best suited to their operating model. With clear insights into both systems—or the ability to harness them in tandem—companies can enhance inventory efficiency and reduce waste.
"A solid grasp of P and Q helps organizations navigate the complexities of inventory management, unlocking pathways to cost savings and improved service levels."
Navigating between these approaches can be critical for sustaining competitive advantages in a market that constantly shifts in dynamics.
Mechanics of the P and Q System
Understanding the mechanics behind the P and Q system is essential for any organization looking to finely tune its inventory management. The mechanics involve not just calculating numbers, but also having a clear grasp on how these calculations influence broader business operations. Essentially, this system hinges on systematic reviews and the flow of goods, which, if managed properly, can lead to significant cost reductions and enhanced stock availability.
Inventory Control Procedures
Reorder Point Analysis
Reorder point analysis is a cornerstone of inventory control. It helps businesses determine exactly when to restock an item based on its usage rate. The key characteristic of this process is its ability to signal when inventory levels dip below a predetermined threshold. It’s popular because it offers a proactive way to prevent stockouts, thereby ensuring that a company can meet customer demand no matter what.
One unique feature of reorder point analysis is its dependability on both sales velocity and lead time. Using historical data, businesses can accurately calculate their reorder points, which ultimately aids in better inventory management. The advantages here are clear: minimizing both excess stock and shortages maintains operational efficiency. However, a drawback could be an over-reliance on historical trends, which may not always predict future demand accurately.
Lead Time Considerations
Lead time considerations play a vital role in inventory control, influencing how businesses anticipate and manage stock needs. The essence of lead time lies in understanding the time frame from placing an order until it arrives for use or resale. This analysis allows firms to align their stock levels with expected delivery times.
Highlighting the importance of lead time is its capacity to enhance reliability in inventory replenishment strategies. Companies that effectively monitor and adjust their reorder points based on lead time tend to avoid pitfalls associated with delays. A unique aspect here is the variability of the lead time, which can impact procurement strategies. On the flip side, one significant disadvantage arises when lead times fluctuate unpredictably, causing challenges in planning.
Order Quantity Determination
Order quantity determination is another pivotal element of the inventory control puzzle. It involves calculating the optimal amount of stock to order so that costs are kept at bay while meeting customer demand. The defining feature of this process is its critical role in balancing holding costs and ordering costs. Basically, it becomes a game of numbers where the goal is to minimize expenses while still having enough stock on hand.
The benefit of thoroughly analyzing order quantities is that it prevents overstocking, which can tie up cash flow unnecessarily. Moreover, it can lead to improved negotiation power with suppliers when large orders are strategically placed. However, there are caveats; miscalculating order quantities can lead to either surplus inventory or stockouts, both of which can adversely affect profitability.
Data Requirements
Data accuracy is crucial when implementing the P and Q system, as it directly impacts how well the mechanics function. A solid data foundation helps businesses make informed decisions regarding inventory levels and forecasting.
Historical Sales Data
Historical sales data is a key resource for any effective inventory management system. It provides insights into past buying behaviors, enabling businesses to forecast future demands accurately. The main characteristic of relying on historical sales data is its predictive power, allowing firms to plan ahead based on previous patterns. This makes it beneficial for maintaining optimal stock levels in the face of changing demand.
One unique advantage of leveraging historical sales data is its active role in identifying seasonal trends. Companies can stock up during peak shopping seasons based on this readily available information. However, a disadvantage here is that outdated data can lead to inaccurate forecasts; trends change, and relying too heavily on the past can hinder adaptability.
Inventory Turnover Ratios
Inventory turnover ratios are another essential component that illustrates how well inventory is being managed. This ratio measures how frequently inventory is sold and replaced over a specific period, providing benchmarks for evaluating operational efficiency. A notable characteristic of this metric is its ability to highlight inefficiencies in stock levels or purchasing patterns.
Using inventory turnover ratios can be highly advantageous as it helps businesses maintain an agile inventory system that meets demand without excessive stock. Additionally, understanding turnover can illuminate which products perform well and which ones do not. However, context is key; sometimes lower turnover ratios can point to larger issues, such as market changes or misaligned product offerings. Therefore, interpreting these ratios requires careful consideration of the broader market dynamics.
Advantages of the P and Q System
The P and Q system stands out as a beacon in inventory management for several reasons. When organizations adopt this system, they can derive numerous benefits that ultimately lead to better operational efficiency and enhanced profitability. Here, we will delve into these advantages in detail, which are pivotal for effectively managing inventory.
Cost Efficiency
Cost efficiency is arguably one of the most compelling advantages of the P and Q system. By breaking down inventory control into two distinct approaches—periodic reviews and continuous assessments—companies can fine-tune their purchasing strategies. For instance, a business that adopts the periodic review strategy can schedule bulk orders at advantageous times, capitalizing on supplier discounts. The continuous review, on the other hand, enables firms to maintain optimal stock levels, thus avoiding overstocking which often results in excess handling costs.
In essence, cost savings can emerge from reduced holding costs and minimized stock obsolescence. However, it’s essential to gather accurate data to support this system. Poor data can lead to misplaced confidence in generated forecasts, resulting in unnecessary expenditures. With solid data management, organizations can streamline their expenses, achieving a favorable cost-benefit ratio.
Improved Stock Availability
Another significant benefit of the P and Q system is improved stock availability. In a world where customer expectations rise incessantly, the ability to provide desired products when needed can make or break a business. Transitioning to a P and Q system promotes better reaction times to consumption patterns. For example, if a particular item is selling like hotcakes, continuous reviews allow a business to quickly restock its supplies based on real-time data.
This agile response often leads to higher customer satisfaction and retention rates. More so, with a well-implemented P and Q system, companies can strategically plan their stock levels to match projected sales cycles, thus ensuring no vital product is ever out of reach.
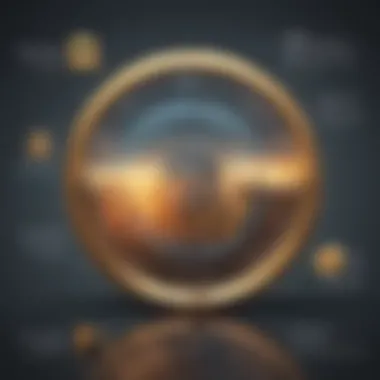
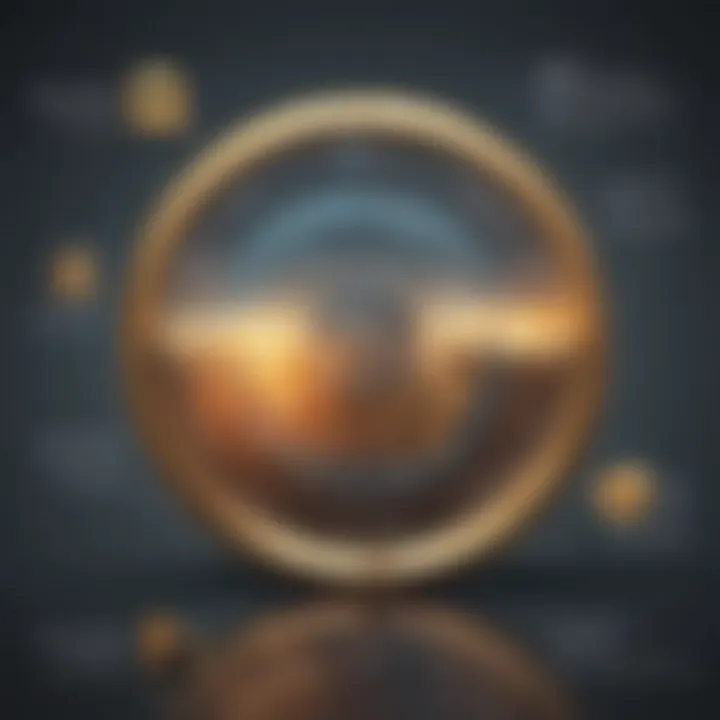
"Stockouts can be more detrimental than overstocking. Losing a sale today might mean losing a customer forever."
Enhanced Decision-Making
The P and Q system also facilitates enhanced decision-making, a necessity in today’s data-driven marketplace. By utilizing detailed data inputs and rigorous analysis, businesses can leverage analytics software to interpret inventory levels and forecast future demand with remarkable accuracy. An organization that relies on informed decision-making can pivot smoothly in response to market fluctuations.
Also, when managers follow the P and Q guidelines, they can make sound decisions about resource allocation. For instance, if specific products consistently demonstrate high demand, a business can prioritize these in production and distribution, directing funds and labor where they matter most. Not only does this ensure efficiency, but it also improves financial performance by directing resources to the most profitable areas.
Challenges in Implementing the P and Q System
The P and Q system of inventory management, while offering a structured approach to stock control, does not come without its hurdles. Understanding these challenges is crucial for businesses attempting to integrate this system effectively. Addressing these obstacles from the outset can lead to enhanced operational efficiency and help organizations achieve their inventory management goals.
Data Accuracy and Management
One of the cornerstones of effective inventory management is having high-quality data. In the realm of the P and Q system, data accuracy becomes a pivotal concern. Without reliable data, organizations face significant risk of making misguided decisions. For instance, inaccurate sales forecasts can lead to the under-ordering of critical stock, causing potential stockouts, or over-ordering, which ties up capital unnecessarily.
To ensure that the P and Q system operates efficiently, business must establish rigorous data collection processes. This entails regularly monitoring stock levels, sales patterns, and lead times—then weaving that information into inventory strategies. Notably, leveraging advanced technologies such as automated systems can provide real-time data updates, driving precision in inventory control.
Challenges with data management can include:
- Data silos: When departments operate in isolation, creating gaps in data sharing which can lead to inconsistencies.
- Human error: Manual data entry is prone to mistakes. Such inaccuracies can mislead reorder decisions.
- Inconsistent inventory audits: Failing to conduct regular inventory checks can result in discrepancies between the recorded and actual stock.
Resistance to Change
Change—particularly in an organizational context—often meets resistance. This phenomenon is evident when introducing the P and Q system, as employees may be hesitant to shift away from familiar practices. Resistance can stem from a variety of sources, including a lack of understanding of the new system, fear of increased workload, or concerns about job security amidst automation.
Engagement and education are keystones to overcoming this challenge. By communicating the benefits of the P and Q system and how it can streamline workflows, organizations can help alleviate fears. Consider offering training sessions that not only explain the mechanics but also showcase success stories of implementing such systems. When team members see the tangible advantages—like reduced effort in inventory tracking—they may be more willing to embrace change.
"Effective change management is about addressing the human side of the equation, fostering a culture of adaptiveness."
Cost of Technology and Training
While the P and Q system promises efficiency, it's important to account for the upfront costs associated with technology and training. Investing in new software or hardware can represent a significant financial commitment for companies. Additionally, budget allocations should also consider ongoing costs for system upkeep and updates, as technology evolves quickly.
Training employees for the new system is another cost factor. Whether companies choose in-house training or external courses, both options require financial and time resources. Moreover, the learning curve may temporarily decrease productivity as personnel acclimate to the new processes.
To mitigate these costs, businesses should weigh the potential return on investment against the expense involved. Organizations may find that with improved efficiency and reduced stock costs over time, the initial outlay is more than justified. As a practical matter, phased implementation can also help ease the transition, allowing a portion of the workforce to smooth out the implementation while others continue with existing processes, dispersing costs across time rather than incurring steep immediate expenses.
Integration with Other Inventory Systems
In today’s rapidly changing business environment, the ability to integrate the P and Q system with other inventory frameworks is crucial. This integration is not just beneficial; it’s often necessary for maintaining efficiency and effectiveness across various sectors. When two or more systems work in harmony, they produce a synergy that can vastly improve outcomes in inventory management.
Comparative Analysis with EOQ
The Economic Order Quantity (EOQ) model is a foundational approach in inventory management. While both P and Q systems serve the purpose of maintaining stock levels, they do so differently. The EOQ model focuses primarily on minimizing total inventory costs, including order costs and holding costs. It relies on the predictable nature of demand and fixed costs, making it less flexible when compared to the P and Q systems.
In contrast, the P and Q approach allows for adjustments according to fluctuating market conditions. For instance, if a retail store observes unexpected spikes in demand, the periodic reviews inherent in the P system can trigger timely orders that EOQ wouldn't accommodate.
Understanding both systems enables businesses to harness the advantages of each, enhancing adaptability while keeping costs low.
Key differences include:
- Order Frequency: P systems review stock levels at regular intervals, whereas EOQ orders are made based primarily on calculated demand.
- Cost Considerations: EOQ minimizes costs during stable demand, while P and Q systems account for variability in demand, making them more adaptable.
- Data Utilization: While EOQ relies on simple historical demand data, the P system requires more robust data analytics to inform decisions during review periods.
P and Q in the Context of JIT
Just in Time (JIT) inventory management strives to minimize holding costs by scheduling orders precisely when they are needed. The P and Q systems can complement a JIT framework, enhancing responsiveness without sacrificing efficiency. In a JIT operation, maintaining optimal stock levels through periodic reviews is vital. By integrating the P system’s periodic demand assessments, JIT can capitalize on real-time data insights that can predict needs with far more accuracy than traditional methods.
Moreover, while JIT focuses on reducing excess inventory, the P and Q model ensures that sufficient stock is available during demand peaks. By planning for the unpredictable, organizations can leverage the strengths of both systems, creating a more resilient inventory management strategy.
Leverage of Technology
The advent of technology has been a game-changer for inventory management systems. The ability to leverage sophisticated data analytics tools and automated systems can enhance the effectiveness of the P and Q model. Companies can use software that integrates real-time sales data, inventory levels, and lead times, allowing for better decision-making.
- Cloud-Based Inventory Solutions: These platforms provide up-to-date visibility across the supply chain, which is essential for effective implementation of both P and Q systems.
- Artificial Intelligence: By employing AI, businesses can predict future inventory needs based on past trends. This predictive capability enhances the periodic assessments in P and Q systems.
- Integration with ERP Systems: Combining P and Q frameworks with Enterprise Resource Planning (ERP) systems provides a holistic view, helping businesses manage resources, timing, and quantities across all departments.
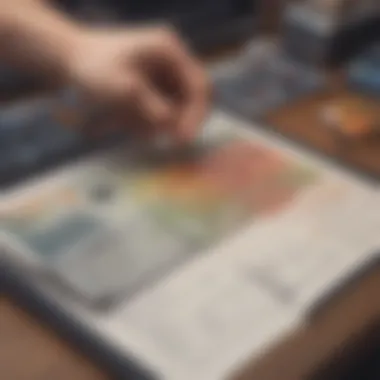
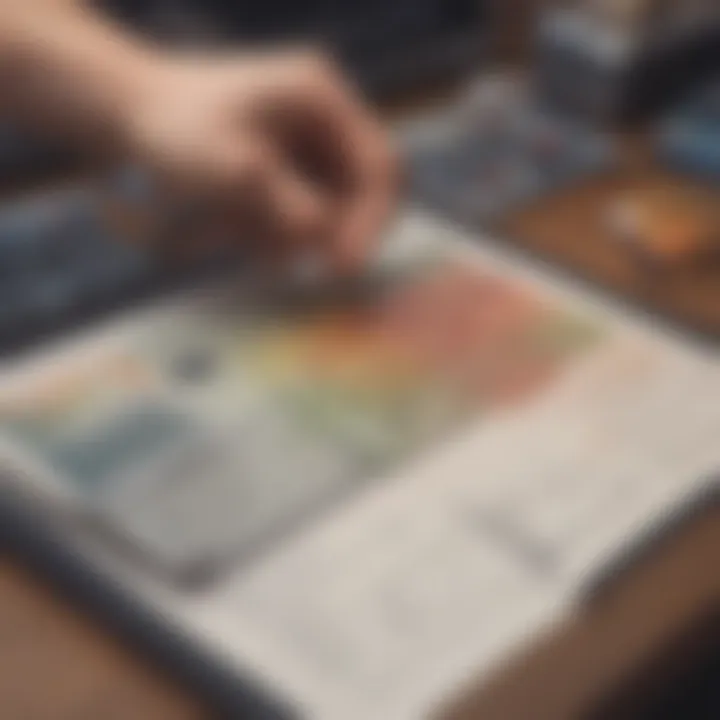
Case Studies: Successful Applications
The significance of case studies in the realm of the P and Q system of inventory management cannot be overstated. In this section, we unpack how real-world examples provide invaluable insights into the practical application and effectiveness of the P and Q methodology. These case studies demonstrate not only the tangible benefits but also the challenges faced by businesses as they integrate these systems into their normal operations.
By analyzing these scenarios, we expose the nuts and bolts of the P and Q framework in action, providing prospective adopters—be they investors, financial advisors, or entrepreneurs—with a clearer picture of what to expect and consider when implementing this system. The value of practical narratives lies in their ability to contextualize theory, showing how variations in approach can yield diverse outcomes in different sectors.
"Real-world examples often serve as the best teachers, illuminating the path for those willing to learn from the successes and missteps of others."
Retail Sector Insights
In retail, managing inventory effectively is often the fine line between profit and loss. Consider a large chain like Target, which implemented the P and Q system to enhance its inventory management. By regularly reviewing stock levels (the periodic aspect) and continuously monitoring sales velocity (the continuous aspect), the chain achieved significant improvements in both stock availability and cost efficiencies.
One clear benefit observed was the reduction in excess inventory, which previously led to hefty markdowns. By employing data analytics to project demand, Target was able to establish optimal reorder points, thus minimizing overstock issues. Moreover, staff were trained to interpret real-time data, ensuring quicker responses to inventory fluctuations. This case demonstrates the integration of advanced technology with the P and Q system, underscoring the necessity of aligning software capabilities with operational needs.
Manufacturing Implementations
Turning our gaze to the manufacturing sector, the automotive company Toyota serves as a compelling example. With its commitment to lean manufacturing, the company adopted a tailored version of the P and Q system that fits its just-in-time (JIT) production model. By embracing periodic reviews for inventory levels of components, Toyota was able to smooth out production flow and ensure efficiency.
The beauty of this approach lay not only in inventory management but also in how closely it related to quality control. When defects were identified in components, Toyota promptly adjusted its order quantities and frequencies to prevent disruption. The direct feedback loop established through their data systems allowed them to function more responsively compared to traditional systems.
In both sectors, these use cases reveal a common thread: successful implementation of the P and Q system hinges on data accuracy and proactive management. As businesses forge ahead with their inventory strategies, it's crucial they learn from these experiences.
The insights gained from retail and manufacturing not only contribute to the body of knowledge surrounding the P and Q framework but also emphasize its adaptability to different industry dynamics. This is precisely why case studies are integral in embodying theories learned into actionable insights for those leveraging the P and Q system.
Future of Inventory Management: The Role of P and Q Systems
As we move forward, the landscape of inventory management is evolving at a rapid pace. The P and Q systems are becoming increasingly vital in navigating these changes. Adapting to new technologies and sustainability requirements is no longer a choice but a necessity. This section delves into the roles that P and Q systems play in molding the future of inventory management, highlighting their significance in contemporary settings.
Evolving Technologies
In this digital age, technology pervades every aspect of business. For P and Q systems, advancements such as artificial intelligence, machine learning, and real-time data analytics are game changers. These tools facilitate precise forecasting and enable more informed decision-making. Businesses can analyze patterns in purchasing behavior with remarkable accuracy, allowing them to adjust their inventory levels proactively.
For instance, a retail chain using AI-based tools can dynamically manage stock levels based on factors like seasonality, market trends, and economic fluctuations. This allows for a more bespoke inventory approach compared to traditional methods, where stock levels were often generic and less responsive to changes.
Moreover, technologies such as IoT devices are also making their mark. Sensors can provide real-time insights into inventory levels, ensuring that businesses reach out for supplies only when necessary. This means companies can operate leaner, saving on both storage costs and unnecessary purchasing. Essentially, technologies are enhancing every facet of the P and Q systems, enabling businesses to respond sharply and intelligently to the marketplace.
"The correct integration of technology with P and Q systems significantly boosts operational efficiency and helps maintain agility in stock management."
Sustainability Considerations
Sustainability is more than a trend. It’s now a fundamental principal shaping business strategies worldwide. The adoption of P and Q systems within this framework promotes responsible resource management. With a keen focus on minimizing waste and optimizing stock levels, these systems align with sustainability goals that many companies now prioritize.
One aspect is the reduction of excess inventory, which may ultimately lead to waste. By refining their stock control measures, companies can reduce overproduction and decrease the energy and resources associated with manufacturing, handling, and disposing of unsold goods.
Here's how businesses can integrate sustainability with P and Q systems:
- Emphasizing Local Sourcing: Focus on local suppliers can enhance sustainability and decrease transportation emissions.
- Utilizing Eco-friendly Packaging: This creates less waste and promotes a positive brand image while aligning with consumer values.
- Implementing Circular Economy Practices: Encouraging recycling and reusing materials can support eco-friendliness.
In sum, the future of inventory management lies in a cohesive blend of evolving technologies and sustainable practices, underpinned by P and Q systems. Embracing these elements effectively positions companies not only to thrive but also to contribute positively to environmental goals.
Epilogue
In today's fast-paced commercial landscape, the role of inventory management cannot be overstated. The P and Q system stands as a strategic methodology that directs businesses towards maintaining optimal stock levels while minimizing associated costs. This article emphasizes the significance of employing such frameworks to refine efficiency and responsiveness to market demands.
Summary of Key Points
The exploration of the P and Q system reveals several significant takeaways:
- The Periodic Review (P) helps organizations assess stock levels at regular intervals, facilitating better planning and forecasting.
- The Continuous Review (Q) allows for real-time inventory tracking, leading to agility in restocking items as soon as they hit a predetermined reorder point.
- Despite its numerous benefits, implementing the P and Q system poses challenges, primarily in terms of data accuracy and the need for skilled personnel to manage the process effectively.
- The integration of P and Q systems with existing technology, alongside traditional methods like EOQ and JIT, can lead to improvements in supply chain performance and sustainability initiatives.
This concluding section points towards a holistic understanding of inventory management strategies. Businesses that leverage the P and Q system not only enhance their operational capabilities but also set a foundation for long-term success, driven by informed decision-making based on robust data analysis.
Final Thoughts
As the demand for efficient inventory solutions grows, navigating the complexities of the P and Q system can offer businesses a competitive edge. The synthesis of technology and inventory frameworks is rapidly evolving, making it crucial for stakeholders—be they investors, entrepreneurs, or analysts—to stay informed.
The insights offered from this article present not just a blueprint for inventory management but also a call to action. Companies must embrace change and continually assess their methods to harmonize profitability with efficiency. The future landscape of inventory management will likely be defined by those who can adeptly balance these elements, ensuring their operations are both responsive to market dynamics and sustainable in the long run.
"In every business, stock control is not just a function; it’s the lifeblood that keeps the organization in motion."
For more on the interrelation of business practices and inventory management, consider resources from Wikipedia or Britannica.